Process Flow
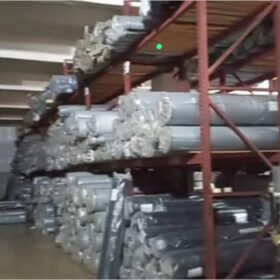

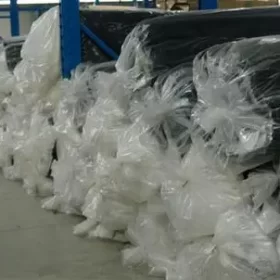
1. Fabric Store
For a bulk production industry, it is essential to maintain a well-organized and well-equipped inventory system. The main responsibility of the fabric store department is to store all the raw materials, especially fabric necessary to produce garments. This department is subdivided into three sections.
Storing fabric in a denim production factory is a crucial step to ensure that the raw materials are protected and maintained in optimal condition until they are used in the manufacturing process.
2. Pattern Making & Digitization
Main task is done here which is to observe the trend of fabric after stitching, Problems during stitching are identified before bulk starts and all settings of machines and gauge sets are finalized here. It minimizes the risk factor in bulk production as all the same work is done here as in bulk; it is a type of preventive action. The samples prepared here are known as PCR which stands for Production Control Run/Production Confirmation Run and commonly known as Pre-Production Samples. The main jobs of this department are to check the first-time marker measurement, before-wash, and after-wash measurements, after comparing before and after-wash amendments are recommended, and shrinkage decisions for the bulk production taken.

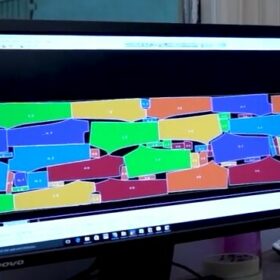

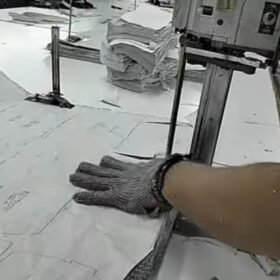
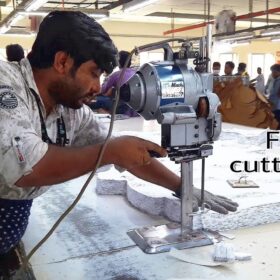

3. Cutting Process
Cutting is the process to separate fabric parts as replicas of the pattern pieces in the marker plan.
The most important and crucial process in the garment industry is cutting process. There is a general saying that cutting makes a company or breaks a company which shows the importance of cutting process. Its fault can not be tolerated and any mishap in cutting will result in wastage of fabric. If during cutting by mistake a pattern is cut wrongly e.g. short length or unwanted cut on the pattern then what will happen? Definitely that mistake will an impact to the whole spread and all pieces of that specific part will be damaged and would not be used resulting in waste of fabric, and fabric is money so finally we will get a loss in terms of money. Hence this process should and must be handled very carefully to avoid any nonconformance to the plan.
4. Stitching Process
The stitching department is the backbone of all production departments. Before discussing the operations of stitching I would like to share some information about some basic terminologies.
Stitch
A stitch is a specific configuration of sewing thread in a repeated unit to make a seam or stitching.
Stitching
Stitching is the series of stitches used to finish the edges or for decorative purposes on a single or more than one ply of material







5. Washing Dry Process
Dry Processes
These processes are handled with dry like sand, sandpaper, etc. as inputs to give a special look to the garment. There are main three dry processes that are used in industry;
- Scraping
- Grinding
- Whiskers
- Spray
- Ripping
6. Washing Wet Process
The washing wet process is a crucial step in denim manufacturing that gives jeans and other denim garments their distinctive look and feel. This process involves washing, distressing, and finishing the denim fabric to achieve various effects like stone-washed, acid-washed, vintage, or distressed looks.
- Jeans or denim garments are loaded into industrial washing machines. Depending on the desired effect, multiple pairs of jeans can be loaded together.
- The denim garments go through a series of washing cycles in large industrial washing machines.
- After the desired wash cycle is complete, the denim garments are thoroughly rinsed to remove excess dye, chemicals, and debris.

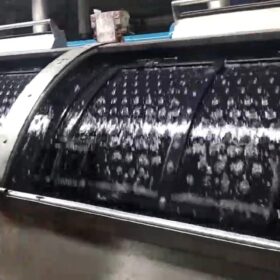
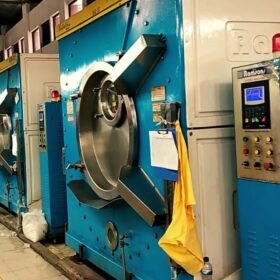

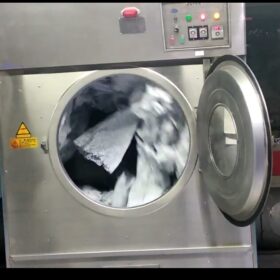
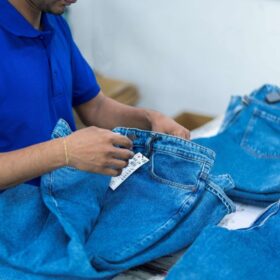


7. Finishing & Packing
The garments received from the finishing floor are sent first for size stickers, hang tag clips, and spare kit (if required) attachment. Then garments go for leg stickers if necessary and a person standing at the end makes sure that no garment is missed for the necessary stickers. After this, ratio-wise sizing is performed, and then the shading process is to make families of available shades to make it possible for one shade would be packed in one carton. After shading, according to the customer’s instructions garments are packed first in poly bags and then in cartons.
When garments are packed, all required information is pasted on the carton plus a barcode according to the customer’s demand. A carton barcode sticker is optional but per garment, a barcode sticker is a must because an open price is not offered. After packing, an internal audit is conducted and if the internal auditor is satisfied then the company calls the external audit for a final audit after the final audit, the order is ready to ship.